During my recent trip to China, the STH team had the opportunity to take a bullet train from Shanghai to Jinan to tour the Inspur Intelligent Factory. Seeing Inspur System’s website, in late 2018, there were pictures of robots putting servers into racks. During a meeting with a company, I asked if they are real. Not only did they say that those videos were of an actual manufacturing facility, but we went a step further. Inspur sponsored our trip to Jinan, we got a film crew, and I received permission to tour the factory. This factory makes servers for hyperscale cloud service providers and is a view we rarely get to see.
Heading to Inspur’s Intelligent Factory
Since the trip from IPF 2019 in Shanghai to Jinan took us over six hours by train and taxi, we stayed the night in downtown Jinan. Across from the hotel, we saw an Inspur building that I mistakenly thought is where we were going in the morning.
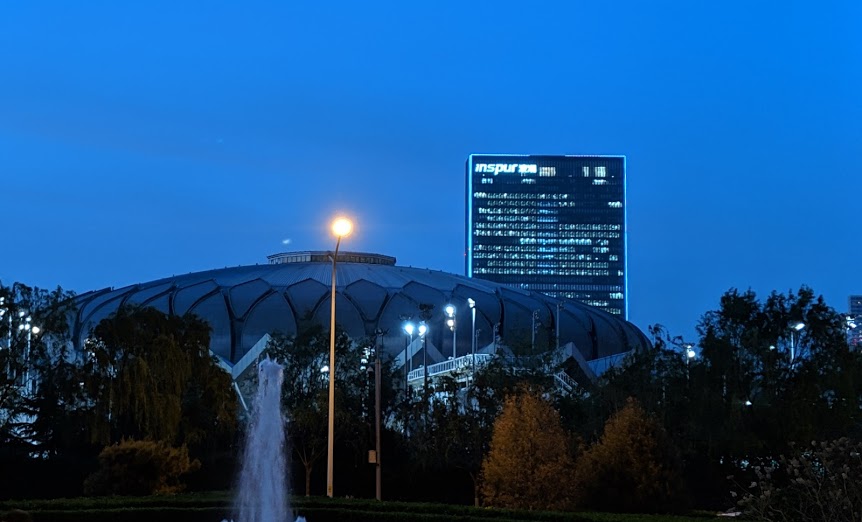
Instead, I was told that building we saw downtown was just a local office for the company headquartered in Beijing. In the morning, we hopped in a taxi and about 40 minutes later we were at Inspur’s manufacturing campus.
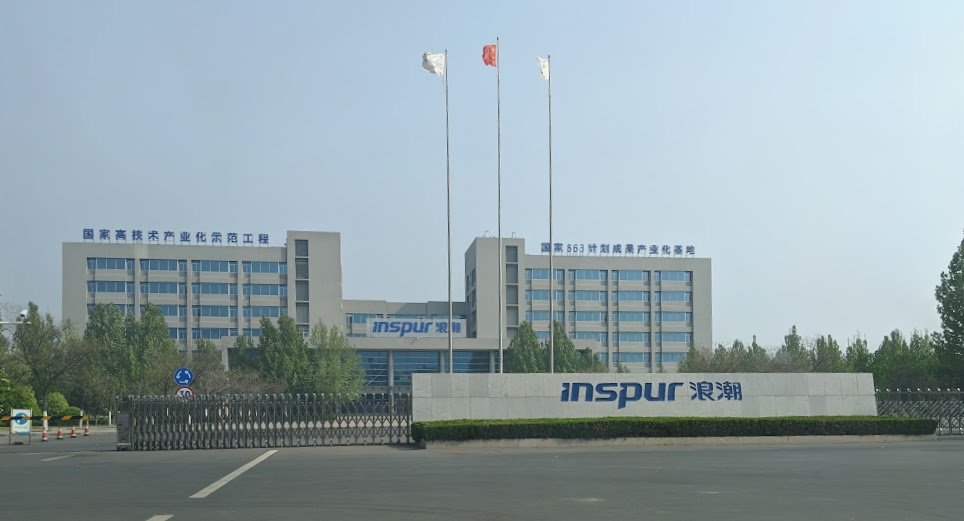
As we arrived, and just outside the facility, we saw grass basketball courts which is very cool to see for a basketball fan.
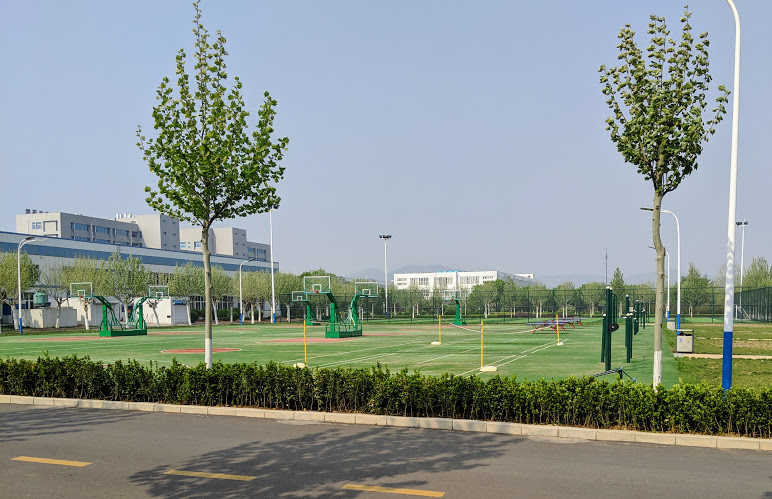
Inside, in one of the lobbies, there were a number of Inspur products. Although there were current generation products on display, I wanted to highlight two. The first is one of the company’s UNIX systems called the Inspur TS-K1. In the video, you may see one of these having a backplane installed later.

The other machine I wanted to highlight was an older PC complete with 5.25″ floppy drives sitting next to the company’s Chinese character pager. These were in the showroom to pay homage to Inspur’s heritage.
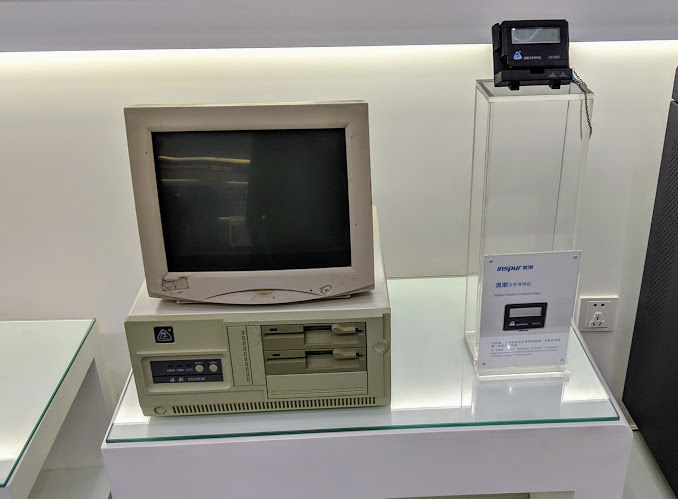
With that, it was time to head into the factory and start our tour.
Touring the Inspur Intelligent Factory
Our Inspur Intelligent Factory tour starts with walking through the dust scrubbing chamber. This ensures that the manufacturing floor is kept relatively dust-free. Here is the full tour video:
As you will quickly see, Inspur is using a high-degree of automation here with robots doing all sorts of tasks. We are going to break down that video in four parts below.
Starting the process, materials for each node are picked from the warehouse by a picking robot. Batches of different CPU SKUs, memory, hard drives, SSDs, motherboards, chassis, cables, and other components are all stored on shelves and then brought to picking stations. There, materials for each node are quickly placed into RFID tagged bins by hand. RFID tagged bins are then fed through the line and queued for delivery to the floor.
Inspur says this system has greatly sped up the process of picking and verifying parts for batches of servers. Whereas a hundred servers worth of parts previously took several hours, using robots, the process is down to only a few minutes.
The RFID tagged bins are then brought to a node assembly line, by robots. Each bin containing the parts for a complete node are then hand assembled. Once they progress through the line, another robot picks the nodes off of the bins and places nodes safely in a carrier fixture so that the bins can be transported to the rack assembly line.
Although this is not in the video, I was told by William, the factory’s manager, that the company allows its employees to suggest, design, and build tools to aid in the server building process. I came home with one of my favorite tools. This simple tool allows one to securely press memory DIMMs into a motherboard without having to directly touch the modules. If you have ever had to install a few hundred DIMMs before lunch, you know that the thin PCB of DIMMs digs into your fingers. This simple device was made by someone at the factory to alleviate that pressure point.
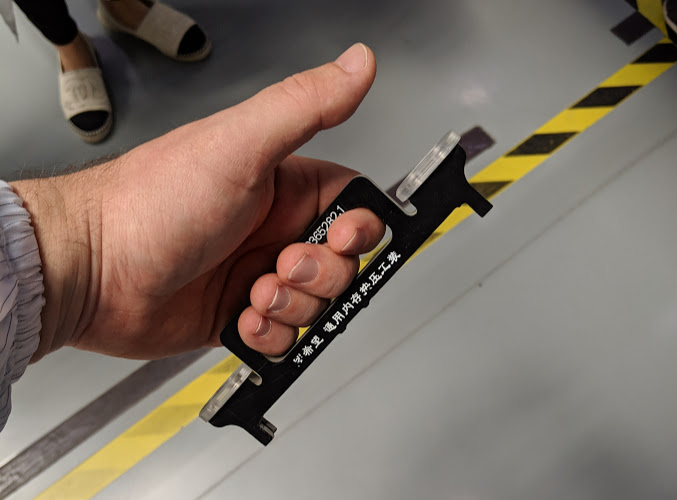
The second line is the rack assembly line. A laser-guided forklift robot picks racks from the warehouse and delivers them to the rack assembly line. From there, other robots do tasks ranging from moving the racks through the line, screwing-in PCBs and other components, and even one other unique twist. A robot brings carriers with completed nodes from the node assembly line to the last stages of the rack assembly line. These are then picked by yet another robot which lines each node up to the rack using laser rangefinders and vision cameras and installs the node into the rack.
Using robots to do tasks such as move materials throughout the warehouse, screw components like PCB midplanes into chassis, and place nodes in racks help to lower potential sources for damage thereby increasing reliability and quality.
After the racks are complete, a laser forklift takes the nodes to the burn-in area. This facility has a 2000m2 burn-in area that is divided into eight separate rooms. Here, the company can vary the temperature, humidity, and power sources to simulate different operating environments. Each rack spends a day to a week being tested at the factory to identify any potential component defects and Inspur has machine learning algorithms to help identify components that may have a higher risk of failure in the field. This allows the company to ensure that the racks leave the warehouse in proper working order so that they can be deployed and run reliably for their customers.
Once the burn-in process is complete, laser forklifts take each rack from the burn-in room and into the final checks before they are packed and shipped to customers.
Final Words
I just wanted to say thank you to the team that made this happen, especially William who shut down his production line so we could take the morning to make this video.
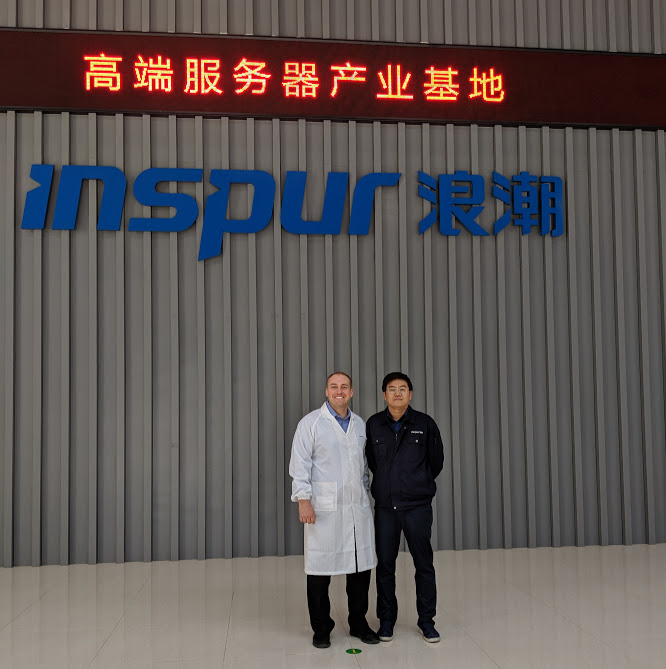
When we left Jinan, we saw plenty of Inspur advertising at the airport on jetbridges. As we were getting on our flight, I stopped to take a quick snapshot of one of these advertisements.
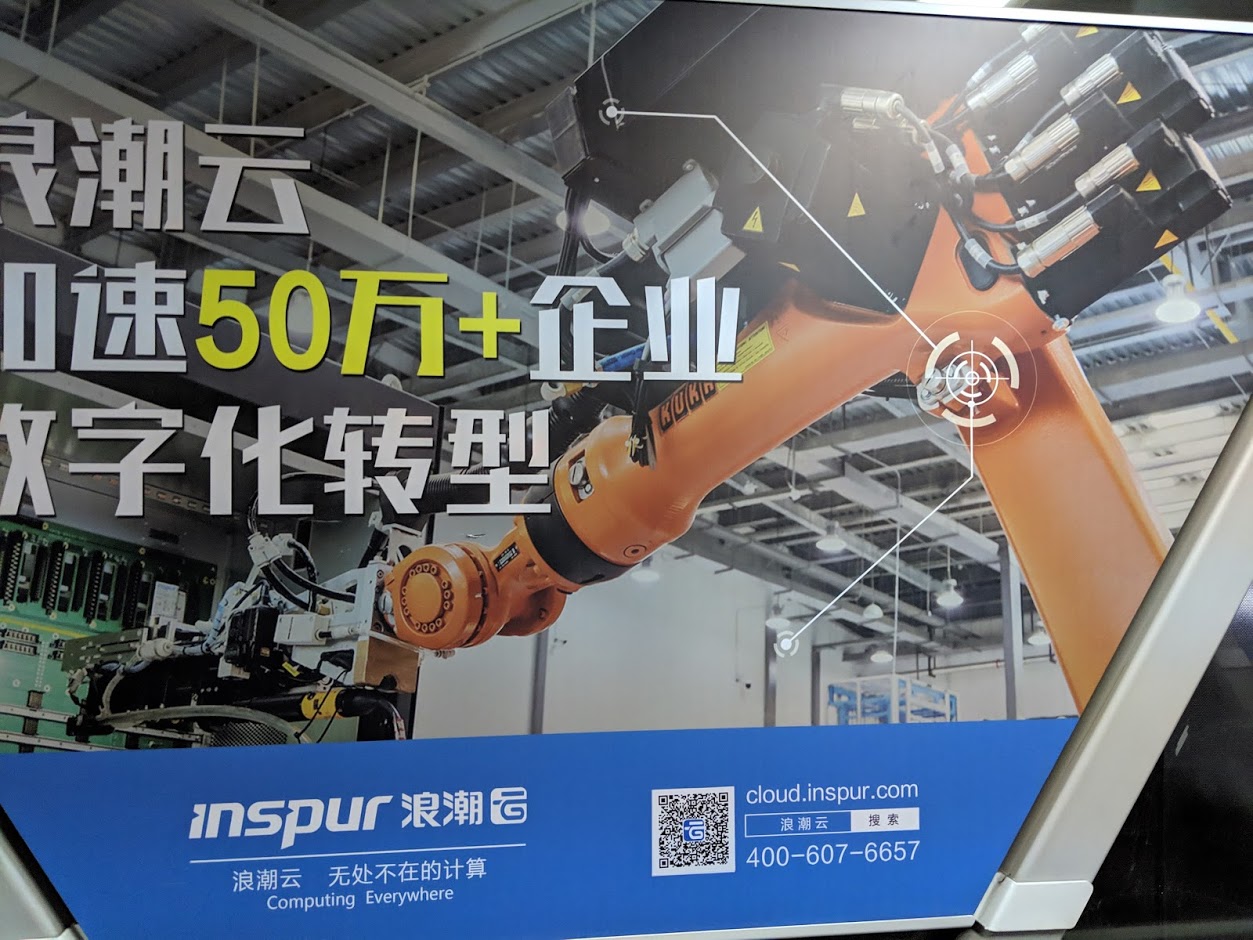
You will notice that the robot pictured in that advertisement is one we saw on the production line earlier that day.
From an industry perspective, I have been to quite a few server manufacturing facilities and this is one of the most advanced in terms of robot usage. Just last year I was at the manufacturing facility of another server manufacturer where each of those steps where a robot was being used in the factory was instead done by hand in hot and humid conditions. The model you see here is how Inspur is producing fully integrated L11 racks that can deploy 10,000 nodes in 8 hours for cloud providers like Baidu.
great article and videos. do more of these
if anyone’s flipping through you want to watch the first video. the other four are just snippets of the first.
I liked the video. Nothing to take away from that. I’d agree with tonyalverez that you should do more.
Inspur needs to get a way to buy test servers easier. We’d buy 1-2 to test ourselves, then consider buying a rack that might be made in a factory like this. We’ve got a 20 person DC ops team and nobody even knew Inspur made servers until we saw them on STH a few months ago with that 8 Nvidia GPU server review.
As long as we don’t let the robots handle the network cabling we can prevent them from upgrading their own brains and implementing 天空网络.
@HankW1972 they were for many years making servers for big label companies. They started selling under their own name only few years ago.