This is a little bit different than our normal server content, but let us discuss a big chip. The 18K Big Sky sensor, built by STMicroelectronics, is so big that only four can be fabbed on a single 300mm wafer. While this is not quite as big as Cerebras Wafer Scale Engine WSE-2 and it is an imaging sensor, it is still very cool.
The Sensor Behind Big Sky
Often, we do not get a lot of information on imaging sensors, so this is really cool. Big Sky is a custom 18K camera to shoot high-resolution video for the MSG Sphere in Las Vegas. The team had to design not just the lenses and camera to capture video played in the Sphere. It also had to design the imaging sensor.
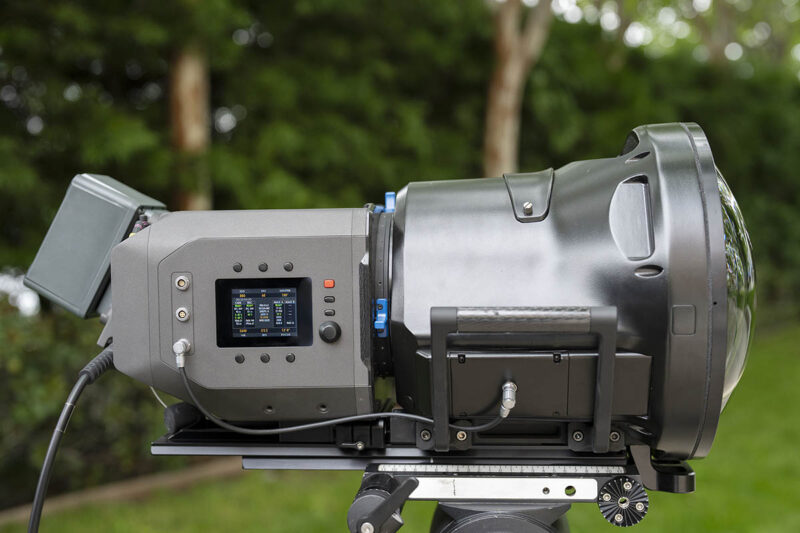
Just for some sense of the size, here is a side-by-side of the Big Sky sensor next to a DSLR sensor.
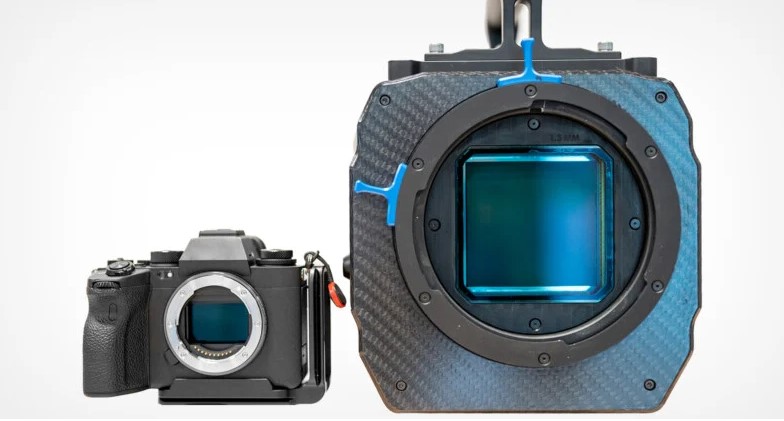
The sensor itself measures around 8.31cm by 9.92cm. ST Micro designed and built the custom sensor during the pandemic so it could be tested and used to shoot for the the Sphere’s launch.
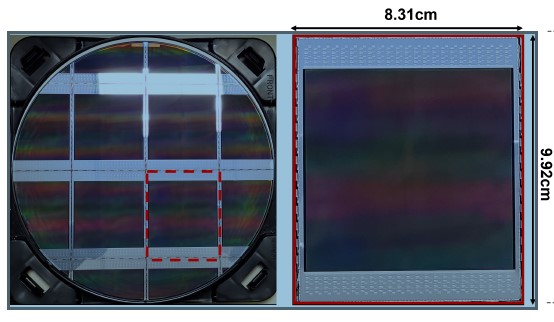
For some sense on how big this is, only four of these sensors can fit on a 300mm wafer.
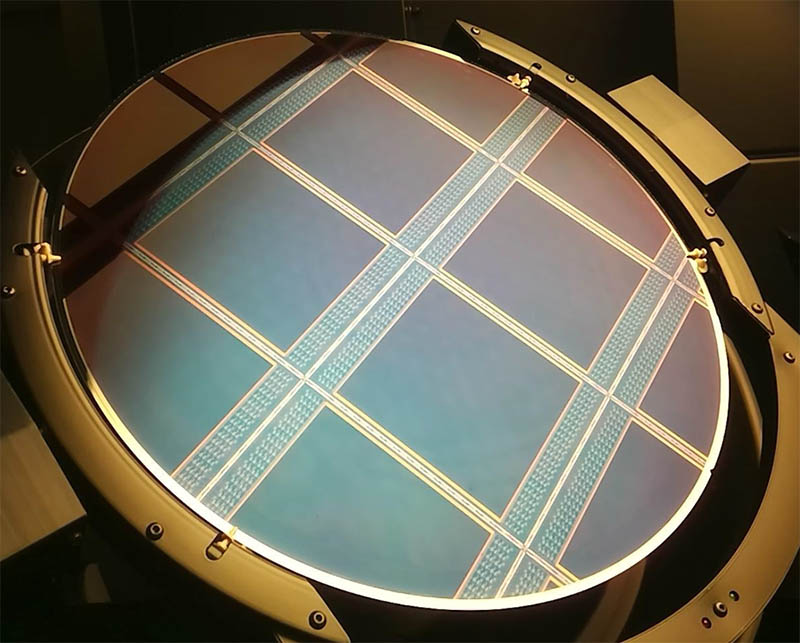
The 316MP sensor is designed to capture video at up to 120fps. With such a high resolution and framerate, the sensor can push around 60GB/s of image data. That requires multiple high-speed optical connections and a custom storage solution. For some sense, a standard 4TB external SSD cannot handle that much data ingest from a speed perspective, and it would be filled after around 67 seconds of footage was shot.
Final Words
While this is not a CPU or GPU, it is still a big chip. We thought the chiphead crowd at STH would get a kick out of the Sphere Entertainment Co. and STMicroelectronics wafer. These things dwarf popular chips like Xeon CPUs, or even the NVIDIA H100 AI GPU. If you get to see a film in the Sphere, then this is the sensor and camera system it is likely shot on.
Very impressive.
Is there any information on the process used to make this?
Afaik the reticle on current steppers only provides about a 20 mm field, which also sets the limits of the Cerebras individual processor. This sensor is almost 4x larger, with no visible seams between elements.
With such big wafers available, they clearly could’ve made a single 36k sensor fill the whole thing!
I guess they used a mask aligners to get around the reticle limit since the entire wafer becomes your reticle
what is a wafter?
Excellent!
“only 4 per wafer” is kind of hilarious on one side, because I doubt they’re making more than a tiny handful of the cameras. I’d be shocked if per-wafer costs had any material impact on their costs.